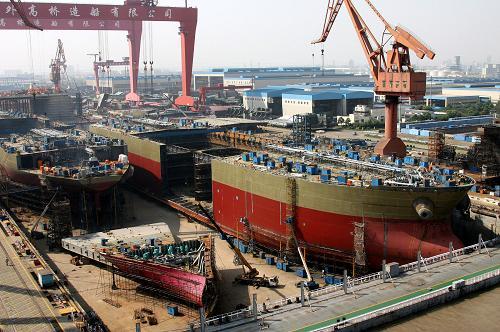
With the rising cost of labor, shipbuilding companies adopt automated welding equipment is the trend. In the future, shipbuilding companies must win the market by improving shipbuilding efficiency, reducing labor costs, reducing management costs, and improving product quality.
While China’s shipbuilding production has won the No. 1 position in the world, it is not unreasonable to find that the labor costs that domestic shipbuilding companies are proud of have been lower than those of Japan’s and South Korea’s advanced shipbuilding companies. In the past two years, the continuous "labor shortage" that has occurred in the southeastern coastal areas of China has been seriously spread to shipbuilding enterprises. China's "demographic dividend" is gradually disappearing. The "labor shortage" of high-skilled personnel in China's shipping companies is particularly prominent. According to survey data, most of the shipping companies in China have large gaps in high-skilled talents, especially in the labor force of shipbuilding production, the proportion of senior workers is often less than 10%, and many companies are even lower than 5%. . Under the new situation, shipbuilding enterprises must use advanced technology and equipment to solidify the advanced process of shipbuilding, in order to reduce the adverse effects of human factors, improve quality, grasp progress, stabilize safety, and win benefits.
It is understood that all developed countries have placed robotics on the top priority in the development strategy of science and technology. In particular, some advanced shipbuilding companies in Japan, South Korea and other countries have achieved remarkable development in the development, development and application of welding robots in shipbuilding. Effectiveness. From the 1970s, Kawasaki Heavy Industries began to develop the first robot. By the late 1990s, several large ship companies in Japan had applied welding robots in batches. For example, various small-scale automatic horizontal fillet welders used in the manufacture of small platforms were used. , Mast-type multi-joint robots, etc.; horizontal automatic gas welding, FAB single-sided submerged arc welding, etc. used for large folding and closing. During this period, the shipbuilding and welding robotization rate of Japanese shipbuilding companies reached 16%, of which 24.6% were small and close together, and 14.5% were parallel in the parallel.
With the rapid development of computer technology, microelectronics, and network technology, while the robotics technology developed rapidly in the 1990s, its manufacturing costs and prices have continued to decline. According to the statistics of the United Nations Economic Commission for Europe, the prices of robots have dropped by about 80% from 1990 to 2000 and labor costs have increased by about 40%.
Since 2001, especially during the peak period of global shipbuilding in the previous few years, the labor cost of China's shipbuilding industry has been rising. However, it is difficult to reduce the current low in the ship market. The high labor cost has become a constraint on our country’s shipbuilding enterprises to become bigger and stronger. One of the important factors. Under this circumstance, accelerating the promotion and application of hull components such as CNC cutting, component robot welding, automatic welding panels, CNC rib bending machines, component robot welding and subsection robot welding, to automate the hull section manufacturing, is to further enhance shipbuilding One of the key factors for production and quality, cost reduction, and shortening the shipbuilding cycle.
With the determination of the direction of green environmental protection, energy conservation, emission reduction and sustainable development in the international shipping industry, shipbuilding companies have been unable to sustain the development model relying on the advantages of intensive labor costs. To win the market, it is necessary to accelerate and widely use automated welding equipment. Improve shipbuilding efficiency, reduce labor costs, reduce management costs, and improve product quality. Only in this way can we have a place in the highly competitive shipbuilding market and achieve development.
5.2:1 or 6.2:1high speed gear system Stainless steel Screw-in Handle for easy installation and removal
|
|
Gear Ratio |
5.2:1 6.2:1 |
Bearings |
3+1 12+1 |
ITEM | Gear Ratio | Ball Bearing | Line Capacity(mm/m;Lbs/yds)-Standard | Line Capacity(mm/m)-Shwallow | OWC |
DSA1000 | 5.2:1 | 3+1BB-10+1BB | 0.18/205 0.20/170 0.25/100; 4/175 6/110 8/90 | 0.12/150 | Y |
DSA2000 | 6.2:1/5.2:1 | 3+1BB-10+1BB | 0.20/245 0.23/180 0.28/115; 4/240 6/160 8/125 | 0.20/150 | Y |
DSA3000 | 6.2:1/5.2:1 | 3+1BB-10+1BB | 0.28/155 0.31/125 0.36/95; 8/180 10/150 12/110 | 0.22/150 | Y |
DSA4000 | 6.2:1/5.2:1 | 3+1BB-10+1BB | 0.28/225 0.31/180 0.36/135; 8/270 10/220 12/160 | 0.24/150 | Y |
Dsa-1 Spinning Reel Series,Micro Fishing Spinning Reel,Saltwater Spinning Reels,Pink Spinning Reel
CIXI DONGSHANG FISHING TACKLE CO.,LTD. , https://www.dongshangreels.com