Fieldbus technology has been developed for nearly 20 years. It has been formulated by planning, research and development, trial operation, and consistent implementation of standards. It has entered the stage of engineering practice. This is a welcome situation. In particular, China's Guangdong Shell China Nanhai project and Shanghai SECCO ethylene project have adopted FOUNDATION fieldbus technology and were contracted by Yokogawa and Emerson-Rosemont respectively. Yokogawa's total contracted 800kt/y ethylene, 240kt/y ethylene glycol, 560kt/y monomer styrene, and propylene oxide (SMPO) are expected to be put into production in December 2005, Yokogawa and CSPC (Shell) Petrochemical, BSF (Bected, Sinopec Engeneering, Sinopec Engineering Company, FosterWheeler) cooperate to jointly design the solutions and structures of the control/information management system. Yokogawa provides FOUNDATION fieldbus equipment and engineering support tools and Intools interface software, etc. .
The project has a large scale. In addition to the FF field instruments mentioned above, there are DCS (including PRM plant resource manager), IPS (instrument protection and safety system), FGS (flame gas system), MAS (mobile automation system), and PIMS (factory information). Management system and OTS (Operation Training System) totaled 100 control stations, 106 operation stations/engineering stations, 399 faceplates, and 17 domains. The fieldbus technology and integrated management and control technologies were all adopted. One of the largest and most technologically advanced projects.
Correspondingly, Fieldbus Foundation released the "Foundation Fieldbus System Engineering Guide" (AG-181) version 1.0 at the end of 2003, a total of 11 chapters. In addition to introductions, references, definitions and documentation, factory acceptance (FAT), and on-site installation, the differences between FOUNDATION fieldbus equipment and conventional analog instruments or previous smart meters are listed in detail, and the main points of engineering practice are defined.
The following FOUNDATION fieldbuses are denoted as FF, and are not specifically designated as FF-H1. As for FF-HSE, the provisions in the main system and software configuration apply to the FCS fieldbus control system composed of FFHSE and FFH1. .
This article will be divided into four parts of field equipment and auxiliary equipment, network segment design, main system, software configuration, introduced to the reader, and talk about the FF system engineering experience.
First, field equipment and auxiliary equipment According to conventional instruments, FF field instrument refers to temperature, pressure, flow, level transmitter, composition analysis online instrument and regulating valve, actuator and so on. However, to become an FF field device, it is necessary to support the FOUNDATION fieldbus function to support the on-line system to execute the relevant program online. It should meet the requirements of the fieldbus registration database and must have the FF "equipment verification" flag to ensure the interoperability of the device.
With respect to field device functional blocks, the general requirement is to be able to form control loops or fieldbus control systems in field devices, ie functional blocks implement control strategies. There are two types of user application blocks, namely control application blocks (or functional block FB). And a device application block, the device application block comprising a resource block (RB) and a transform block (TB). Usually called resource blocks, transform blocks, and function blocks.
Function blocks: To implement the different functions required for the control system, users need to select function blocks according to their actual application requirements. There are standard, advanced and additional 3 types of function blocks, including 10 standard function blocks (or basic function blocks), 19 advanced function blocks, and 5 additional function blocks. Please refer to the FF website for details.
There are certain restrictions on the application of the following function blocks: Al is used in transmitters, AO and PID are used in valves, Dl/DO is used in discrete devices, and FF function blocks only include the appearance of functional blocks and the behavior of external interfaces, and do not include Its internal performance. In addition to the above standard blocks, the concept of an enhancement block and an instantiation block is also proposed, and the instantiation block facilitates interoperability. The structure of the functional block is shown in Figure 1.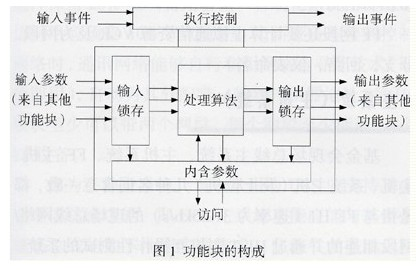
Resource Block: Describes the characteristics of the field device, such as the device name (device type and version), manufacturer, and serial number. Only one resource block can exist in each device. It is the only mandatory block in the FF device. It describes the local hardware object of the field device and its related operating parameters, ie, the information including ID (identity) and basic information related to the status of all resources or resources, including information on whether the device is normal operation and operation, including write protection and supporting simulation. Wait.
Conversion block: It includes information such as calibration date and sensor type. It separates the function from reading the sensor and command output to the local input/output function of the hardware. That is, it can realize the parameterization of the equipment,
Calibration and diagnosis. Each input or output of a device usually has a TB channel. In summary, the conversion block represents the 1/0 characteristics of the field device, such as the characteristics of the sensor and the actuator.
Equipment diagnosis: This is an important function of FF. Field equipment should provide key information for equipment measurement or control process, including basic diagnosis, advanced diagnosis and process diagnosis.
The basic diagnostics are those that can be seen from any process control host. This helps diagnose equipment, communication paths, and common faults in the host. When the diagnostic display device fails, it should be forced to switch to manual. Basic diagnosis is also called public diagnosis.
Advanced diagnostics include all device diagnostics that determine the health of the device without removing the device. Including online and offline methods, scanning scans include dynamic scans and step scans.
Process diagnostics refers to the tests performed while the process is running. It allows maintenance personnel to compare host actions, actuator actions, output device actions, and process actions by changing the output device value to exceed the maximum deviation of its configuration.
An FF device can be two or more logical field devices, or virtual virtual devices (VFDs). The VFD is used to remotely view the local device data described in the object dictionary (OD). It contains the physical and resource data of the device. The management, resource data includes virtual communication resources VCR.
The description of the field equipment power supply, working conditions and factory configuration in the guide is omitted here.
About auxiliary equipment: Main distribution power supply, power regulator, terminator, repeater, junction box. The main distribution power supply converts the 22.0V/l20V AC to a 24VDC power supply, or is powered by a UPS. After the power regulator of each segment, the bus power supply voltage is approximately 1gVDC, which is redundant, isolated, and equally divided. Load, current limit, alarm, etc. In addition, there are two terminators per network segment.
Second, the network segment design FF segment topological tree topology, branch topology and hybrid topology, and clearly pointed out that because it is not suitable for maintenance, do not use daisy chain topology. Tree topology is suitable for retrofit projects, specific areas with high density of field devices, and the use of high-speed Ethernet (HSE); branch topology is applicable to areas that are installed for the first time and have a low density of equipment. Usually, the branch topology is not an economy. Program. The hybrid topology is shown in Figure 2.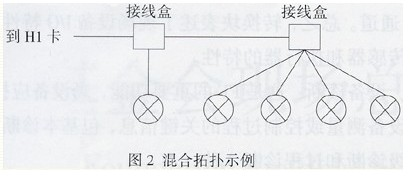
For the use of cable types, the guideline specifies that for the first installation, it is best to use the individually shielded twisted pair and the fully shielded cable with the 18GA (0.8mm2) ITC model and a list of cable characteristics. Special colors should be distinguished from the traditional 4-20mADC cables, and it is pointed out that if the line pairs shield each other from the fieldbus signals and the 4-20mADC signals can be transmitted on the same multicore cable. The cable should be flame-retardant insulation of thermoplastic elastomer (TPE), and its color and polarity should be unified with existing equipment. It should have appropriate electrical area class and can be applied to outdoor cable tray installation. The cable jacket can be used. Flame-retardant polyvinyl chloride (PVC).
If no cable of the above type is used, fieldbus induced signals shall be applied. Tests include signal capture at the outgoing end of the power supply and at the remote end of the cable.
The maximum allowable length of the fieldbus segment is 1900m. Segment length = trunk length + all branch lengths. The above length is a conservative value. The branch length is 1 to 200m. Each branch can only connect one FF device. The recommended branch length is 30m.
Mainline cables, power supplies, grounding and lightning protection, and network segment risk management (level 4 valve and network/network segment) are all clearly defined. With respect to multivariable field devices, multivariable transmitters of the AI ​​function block type can only be used for one control loop, other variables are used only for monitoring, and multivariable transmitters belonging to the MAI function block are used for monitoring only.
The conceptual model of FISCO fieldbus intrinsic safety is jointly completed by the German Federal Institute of Physics and Technology and several internationally renowned manufacturers. In addition to the reference to this guide, the specific project also reads relevant standards and procedures. The purpose of proposing and developing FISCO is to provide power to the fieldbus network/network segment while ensuring that the energy level does not cause an explosion. Due to the limited DC power common to multiple field devices, the long cable and capacitor capacity stored in terminators, traditional intrinsic safety devices and interconnection rules limit the use of intrinsically safe systems. Specifically, the FIS-CO parameters of the EEXiaIIc and EExibIIC/IIB explosion-proof grades are given.
The FOUNDATION fieldbus load is determined by the minimum of the following four parameters: network segment risk management, spare capacity, network segment execution time, voltage drop, and current limit. Spare capacity should be reserved for 25% in the design of the network segment, and a control loop (ie, 1 transmitter and 1 final component) can be reserved for the specific design. The default execution time of the network segment is 1s. It is recommended that the maximum number of devices in a network segment be: the only network segment with a monitor is 12 devices; the network segment requiring a 1s execution time is 12 devices with 4 valves; the network with a required execution time of 0.5 s The segment is six devices with two valves; the network segment requiring a 0.25s execution time is three devices with one valve.
The minimum value determined by the voltage drop and current limit must be analyzed for each FF network segment. The calculated device voltage must exceed the minimum operating voltage of the equipment by 4V (that is, 9+4=13V), which will be added to the network segment in the future. Reserve margin for equipment. Another example is the current of a single factory equipment does not exceed 15mA, the output device current does not exceed 25mA, network equipment does not exceed 16, the network length does not exceed 1000m, and 16 input devices are located at the farthest end of the bus, the total current consumption is 16x15 =240mA. The impedance of the 1kml 8# loop is 44Ω/kn and the line voltage drop is 44x0.24=10.6V. The minimum voltage of the power supply is 10.6+9=19.6V.
The FF network segment also calculates the virtual communication resources VCR and names the network segments, branches, loops, and meters.
Third, the main system (host system)
The FOUNDATION fieldbus host system, host system, FF host, host computer, and system host (and host computer) have the same meanings in several terms. They all refer to the field bus network/segment connected to FFH1 (31.25kb/s). And through the HIST host interoperability testing system. The system should use standard products (standard hardware, system software and firmware), and the system software and firmware should be able to meet the specified requirements after configuration.
The HIST technical specification is FF-569, which is generally supervised by Fieldbus Foundation personnel, but it also points out that for FF host systems that do not support the specified HIST performance, after thoroughly evaluating the performance limitations of the main system, the chief project engineer and project leader should Approve its use in writing. About FF-569 is equipped with the performance and components of the FF host. The host can be a configuration tool, a recording device, an alarm display panel, a human-machine interface, or a combination of functions. These are manufacturers of automation systems other than DCS or large-scale system integrators. The development of products matching FF creates opportunities.
To develop a set of operational test procedures, FF-569 defines a common set of FF host performance metrics that can implement some or all of the performance within the host. These properties include: device tag assignment, device address assignment, configuration of fully-connected master devices, block tag configuration, block instantiation, standard blocks, enhancement blocks, client blocks, function block link configuration, FF alert groups Status, FF alarm processing, FF trend configuration, FF trend processing, device description (DD) service, DD method execution, DD menu processing, DD edit display processing, capability file, etc. In addition, the performance of downloading upgrade software to field devices through the host online will become a host test requirement in the near future.
It also stipulates to the standard products that the information from the FF equipment shall not be mapped into the system by the I/O channel method. When the control strategy is implemented, the functional blocks residing in the equipment may be used directly.
Provisions for spare capacity and expansion of the host system are specified: When configuring the system for all components, at least 10% of spare capacity is reserved for each system. This includes application software, graphics, history, reports, and trends. In the basic system, 10% spare capacity is reserved for various types of I/O. It is recommended to reserve 10% to 50% of the space for the backplane and marshalling terminals. The module reserves 20% to 25% spare capacity. The communication network inside the automation system should reserve 10% of the node address. When a new device is connected to the control network, the communication network can use the network self-addressing technology (plug and play) to assign a unique new controller address automatically. . Each H1 module can have at least two network segments, and each network segment can have at least 16 FF devices.
As a main system, DCS currently used should support the FOUNDATION fieldbus function, that is, the DCS main system function should be able to integrate with the FOUNDATION fieldbus as follows: automatic node addressing; interoperability; use of standard DDL (equipment Description language) Direct configuration of the device; direct integration of FF device operation, maintenance and diagnostics data; adjustment of parameters, modes, alarms and data quality; no commissioning and start-up delays, should be available to existing networks/segments (eg equipment bits New field devices are added in number/placeholder) and all configurations can be performed; without shutting down the network, the configuration of field devices can be realized while the main system is running; a device capability file should be provided.
The main system data transfer function should be able to integrate third-party database systems into fieldbus devices. If you use OPC (OLE for process control), you should ensure that the product passes the "OPC Compatibility Test".
The main system as a configuration tool should provide online and offline configuration tools. The configuration tool should have multi-user and multi-instance capabilities. Requirements for system integration capabilities: All master FF functions, including engineering, configuration, maintenance, and operational display capabilities, should be integrated into a single, seamless main system. Engineering, configuration, maintenance and operational performance should be compatible and seamlessly integrated with conventional analog or discrete I/O, smart HART and dedicated I/O, bus-based I/O and FF systems, and it is recommended that: Do not use only Independent software tools, displays, or programs that target FF and are incompatible with legacy systems. In terms of method and appearance, the main FF configuration should be consistent with the traditional configuration. When the FF function is mapped to a dedicated function block, the internal mirroring or shaded function blocks used by the control system should be completely transparent to the configuration engineer, technical maintenance personnel, and operators. Both configuration and operation should use single, unique and independent function blocks and parameter tag names. Using the same configuration tools, both FF and traditional control strategies are able to save, restore, and partially download the main control system database in a seamless and transparent manner. All these reflect the fact that the Fieldbus Foundation has fully considered the inheritance and inclusiveness of the automation system, protecting the interests of end users, protecting the interests of existing automation equipment manufacturers, and facilitating the integration of new FF products into the automation market. Accepted by the majority of users, this is the trend of PAS development in the process industry automation system for a long time to come.
Off-line FF configuration refers to the FF policy configuration when the network/segment or FF device is not connected. The host can configure all the FF function blocks and parameters and support the technical specifications of the DD service and Common File Format (CFF). Regarding the transparent management macro cycle scheduling, the minimum non-scheduled non-cyclical time is maintained, and at least 70% of the unscheduled non-cyclical time is reserved for the first installation.
There are several aspects of host system redundancy and stability, troubleshooting, maintenance and diagnostics, advanced diagnostics, and computer-based maintenance and evaluation criteria.
Fourth, the software configuration Configuration (Configuration) the definition of the term is: In order to meet the system requirements, the physical installation of the hardware module; or to meet the system requirements of the software option settings. The guide also pointed out that the so-called "configurable" meaning is the ability to select and connect standard hardware modules to create systems; or to modify or change the capabilities of software functions by modifying parameters without modifying or updating the software. These definitions serve as an opening for this section and are very helpful for everyone to understand the importance of software configuration.
During the configuration process, the control system graphics and FF-related graphics should meet the existing standards for end-user graphics and provide a wealth of additional instructions (including device status alarms, FF trends, and alerts).
The FOUNDATION fieldbus node address is the network segment describing the current address of the device. The node address range is 0~255. The allocation is as follows: 0 ~ 15 reserved; 16 ~ 247 is the address used by permanent equipment, the general low number for the upper communication and host interface, some of the high number assigned to online field devices (to improve efficiency, the range is usually reduced); 248 to 251 are addresses for non-permanent devices, such as new or deactivated devices; 252 to 255 are addresses for temporary devices, such as handheld tools.
In addition, device naming, control strategy/module naming, and FOUNDATION fieldbus block naming are stipulated. These are indicated on the P&ID, in which the suffixes and named instances of multiple identical blocks in a device are shown in Figure 3, where In the device TT temperature transmitter 1000, there are two analog input signals respectively labeled with AI_l and Al_2.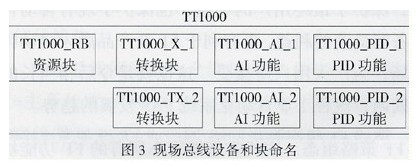
Regarding localization of the control function, the module is named according to the bit number indicated by P&ID. As shown in FIG. 4 , the control block can be implemented in a field device or a main controller. For field-based control, equipment with PID control algorithms should be marked on the corresponding network/network segment drawings and include the bold letter P. For single-loop PID control in field devices, all the functional blocks that make up the control loop are Should reside on the same network segment (usually the PID is placed in the control valve positioner); if it cannot reside on the same network segment, the PID control algorithm can be placed in the main system (such as a DCS control station). For cascade control, the preferred configuration is the positioning of each cascaded loop function block and device on the same network/segment. The primary PID controller should reside in the primary measurement transmitter and the secondary PID control should be Stay in the final component; in another case of cascade control, the primary PID controller resides in the central controller/host, the secondary loop functional block and device reside on the same network segment, and the secondary PID control can reside in the final Components.

When deciding the PID position, execution time, advanced diagnostics, failure modes, and operator access need to be considered. As with conventional control systems, it is also necessary to determine the correct behavior of each control loop fault protection when the loop and equipment failure modes.
Each configuration option and default value should be documented as a guide to the control strategy and reviewed and approved by the end-user engineering representative as it constitutes the configuration basis for the behavior of the equipment and control system under "abnormal" conditions, which is a safety measure for the plant. And reliable operation is very important. The guideline document should highlight the differences between the configuration and operation of FF and non-FF control strategies, and also include configuration options and default values ​​for the main system including the settings, equipment, and asset management software.
The guide documentation should provide descriptions of various typical function blocks and control modules, describe in detail the settings of parameters and the operation of subsequent blocks/modules. The contents of the narrative discussion include parameter configuration, operation of the signal "state", determination of invalid values, and failures. Mode switching, initialization performance, limit performance to prevent reset, etc. Some examples of default settings for instance loops are as follows:
(1) For an invalid PV (process variable), the loop mode should be switched to the manual mode. This state generates an alarm and displays it on the graph. The panel color changes and the data display disappears.
(2) Loop mode should ignore the suspicious PV. This state will not cause an alarm, but it will be displayed on the graph and the panel color will change.
Regarding alarms and warnings, the fieldbus includes 15 alarm priorities and is mapped to the main system. For example, in the DCS, there are no actions (level 1), logs (levels 2 to 4), and low levels (levels 5 to 7). High (8-11), emergency (12-15). The host must support the time synchronization and alarm time stamping of field devices.
Communication errors, misoperations (diagnoses) or malfunctions, on-site equipment will generate warnings. Warnings are the collective name for alarms and events. The alarm is generated and eventually cleared (disappeared), two reports are generated, and only one report occurs. The FF system uses alerts to notify the user of the various states of the device.
The FOUNDATION fieldbus is able to capture the trend of the most recent 165 process variables and status points and provide time stamps for each network/network segment.
Regarding network communication and scheduling, FFHl's data link layer LAS link activator is responsible for the coordination of all communication on the fieldbus, completes token transmission control, and guarantees data transmission services and link time synchronization services, generally in the main control system redundancy. H1 network interface plug-in, its network / network segment execution time, macro cycle, network / network segment scheduling should leave a margin, to ensure that there are enough non-scheduled time in each cycle to transfer non-cyclical (maintenance and configuration) information .
The failure rate of the PID block must be set to a minimum of 3 to ensure that the setpoint tracking action is performed.
Regarding VCR virtual communication relations, or virtual communication resources, when configuring a complex control strategy, it is necessary to pay attention to the number of functional blocks and VCRs supported by field devices and main systems. Under normal circumstances, field devices cannot support more functional blocks and the number of VCRs, so the complex control strategy should be more placed in the main controller (such as DCS control station). In order to clearly see the example shown in Figure 5, first make the following description: The FOUNDATION fieldbus communication model is divided into four levels, namely, the physical layer, data link layer, application layer and user layer, but according to the function has 3 The part, that is, the communication entity, the system management kernel, and the functional block application process, each part communicates information through the VCR, so the virtual communication relationship is the configuration application layer channel and can provide data transmission for the application program. The FOUNDATION fieldbus describes three types of VCR virtual communication relationships: publisher/subscriber, guest/server, and source/receiver. The VCR is included in the Network Management Information Base (NMIB), and the addressing of VFD virtual field device objects is implicitly defined by the VCR in the virtual communication relationship list.
Figure 5 shows an example of a complex control strategy. In the figure, the MIB is the management information base, Prim.Host and Sec.Host are the main sub-hosts, Aleris is the alert, and Trends is the trend. Two AI blocks and PID blocks reside in the same device. AI-l is related to the PID block. AI-2 sends its data to other devices. The VCR requirements are shown in Table 1. The VCR bus is: l ( AI-2)+2(PID)+5(basic device)=8.
In the system engineering guide, it is also required that the host system configuration tool and data should have import/export functions for all function blocks and module data. The formats include: comma separator, Microsoft Excel, text, Microsoft Access, and SQL. The host should be able to download all the function blocks using the imported data. Download features include control functions, scheduling and initialization, exporting and updating external databases. For the operator display, it is required to achieve process visualization, high confidence, safety, ease of use, high utilization, easy maintenance and management, and no need to stop the production process when the software version is upgraded. It also puts forward a series of strict requirements for system management, control and data processing, system configuration tools, and display.
In the face of FF entering the engineering practice stage, China should take the enterprise as its main body, and it must combine the development of FF field instrumentation and main system as well as the work of FF registration and interoperability certification.
The introduction of ethylene engineering to digest and absorb FF application technology in the system engineering guide, also requires the host system configuration tools and data should have all function block and module data import/export capabilities, its format includes: comma separator, MicrosoftExcel, text Microsoft Access, SQL. The host should be able to download all the function blocks using the imported data. Download features include control functions, scheduling and initialization, exporting and updating external databases. For the operator display, it is required to achieve process visualization, high confidence, safety, ease of use, high utilization, easy maintenance and management, and no need to stop the production process when the software version is upgraded. It also puts forward a series of strict requirements for system management, control and data processing, system configuration tools, and display.
In the face of FF entering the engineering practice stage, China should take the enterprise as the main body, and in addition to the FT field instrument and main system research and FF registration and interoperability certification work, we must combine the introduction of ethylene engineering to absorb and popularize FF application technology. Make it play a role in actual process industrial production as soon as possible.
The project has a large scale. In addition to the FF field instruments mentioned above, there are DCS (including PRM plant resource manager), IPS (instrument protection and safety system), FGS (flame gas system), MAS (mobile automation system), and PIMS (factory information). Management system and OTS (Operation Training System) totaled 100 control stations, 106 operation stations/engineering stations, 399 faceplates, and 17 domains. The fieldbus technology and integrated management and control technologies were all adopted. One of the largest and most technologically advanced projects.
Correspondingly, Fieldbus Foundation released the "Foundation Fieldbus System Engineering Guide" (AG-181) version 1.0 at the end of 2003, a total of 11 chapters. In addition to introductions, references, definitions and documentation, factory acceptance (FAT), and on-site installation, the differences between FOUNDATION fieldbus equipment and conventional analog instruments or previous smart meters are listed in detail, and the main points of engineering practice are defined.
The following FOUNDATION fieldbuses are denoted as FF, and are not specifically designated as FF-H1. As for FF-HSE, the provisions in the main system and software configuration apply to the FCS fieldbus control system composed of FFHSE and FFH1. .
This article will be divided into four parts of field equipment and auxiliary equipment, network segment design, main system, software configuration, introduced to the reader, and talk about the FF system engineering experience.
First, field equipment and auxiliary equipment According to conventional instruments, FF field instrument refers to temperature, pressure, flow, level transmitter, composition analysis online instrument and regulating valve, actuator and so on. However, to become an FF field device, it is necessary to support the FOUNDATION fieldbus function to support the on-line system to execute the relevant program online. It should meet the requirements of the fieldbus registration database and must have the FF "equipment verification" flag to ensure the interoperability of the device.
With respect to field device functional blocks, the general requirement is to be able to form control loops or fieldbus control systems in field devices, ie functional blocks implement control strategies. There are two types of user application blocks, namely control application blocks (or functional block FB). And a device application block, the device application block comprising a resource block (RB) and a transform block (TB). Usually called resource blocks, transform blocks, and function blocks.
Function blocks: To implement the different functions required for the control system, users need to select function blocks according to their actual application requirements. There are standard, advanced and additional 3 types of function blocks, including 10 standard function blocks (or basic function blocks), 19 advanced function blocks, and 5 additional function blocks. Please refer to the FF website for details.
There are certain restrictions on the application of the following function blocks: Al is used in transmitters, AO and PID are used in valves, Dl/DO is used in discrete devices, and FF function blocks only include the appearance of functional blocks and the behavior of external interfaces, and do not include Its internal performance. In addition to the above standard blocks, the concept of an enhancement block and an instantiation block is also proposed, and the instantiation block facilitates interoperability. The structure of the functional block is shown in Figure 1.
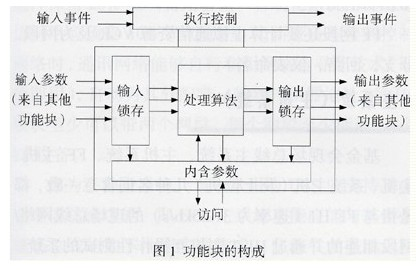
Resource Block: Describes the characteristics of the field device, such as the device name (device type and version), manufacturer, and serial number. Only one resource block can exist in each device. It is the only mandatory block in the FF device. It describes the local hardware object of the field device and its related operating parameters, ie, the information including ID (identity) and basic information related to the status of all resources or resources, including information on whether the device is normal operation and operation, including write protection and supporting simulation. Wait.
Conversion block: It includes information such as calibration date and sensor type. It separates the function from reading the sensor and command output to the local input/output function of the hardware. That is, it can realize the parameterization of the equipment,
Calibration and diagnosis. Each input or output of a device usually has a TB channel. In summary, the conversion block represents the 1/0 characteristics of the field device, such as the characteristics of the sensor and the actuator.
Equipment diagnosis: This is an important function of FF. Field equipment should provide key information for equipment measurement or control process, including basic diagnosis, advanced diagnosis and process diagnosis.
The basic diagnostics are those that can be seen from any process control host. This helps diagnose equipment, communication paths, and common faults in the host. When the diagnostic display device fails, it should be forced to switch to manual. Basic diagnosis is also called public diagnosis.
Advanced diagnostics include all device diagnostics that determine the health of the device without removing the device. Including online and offline methods, scanning scans include dynamic scans and step scans.
Process diagnostics refers to the tests performed while the process is running. It allows maintenance personnel to compare host actions, actuator actions, output device actions, and process actions by changing the output device value to exceed the maximum deviation of its configuration.
An FF device can be two or more logical field devices, or virtual virtual devices (VFDs). The VFD is used to remotely view the local device data described in the object dictionary (OD). It contains the physical and resource data of the device. The management, resource data includes virtual communication resources VCR.
The description of the field equipment power supply, working conditions and factory configuration in the guide is omitted here.
About auxiliary equipment: Main distribution power supply, power regulator, terminator, repeater, junction box. The main distribution power supply converts the 22.0V/l20V AC to a 24VDC power supply, or is powered by a UPS. After the power regulator of each segment, the bus power supply voltage is approximately 1gVDC, which is redundant, isolated, and equally divided. Load, current limit, alarm, etc. In addition, there are two terminators per network segment.
Second, the network segment design FF segment topological tree topology, branch topology and hybrid topology, and clearly pointed out that because it is not suitable for maintenance, do not use daisy chain topology. Tree topology is suitable for retrofit projects, specific areas with high density of field devices, and the use of high-speed Ethernet (HSE); branch topology is applicable to areas that are installed for the first time and have a low density of equipment. Usually, the branch topology is not an economy. Program. The hybrid topology is shown in Figure 2.
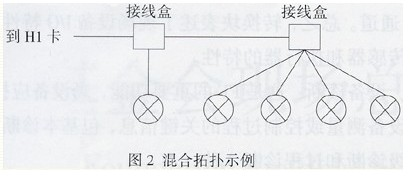
For the use of cable types, the guideline specifies that for the first installation, it is best to use the individually shielded twisted pair and the fully shielded cable with the 18GA (0.8mm2) ITC model and a list of cable characteristics. Special colors should be distinguished from the traditional 4-20mADC cables, and it is pointed out that if the line pairs shield each other from the fieldbus signals and the 4-20mADC signals can be transmitted on the same multicore cable. The cable should be flame-retardant insulation of thermoplastic elastomer (TPE), and its color and polarity should be unified with existing equipment. It should have appropriate electrical area class and can be applied to outdoor cable tray installation. The cable jacket can be used. Flame-retardant polyvinyl chloride (PVC).
If no cable of the above type is used, fieldbus induced signals shall be applied. Tests include signal capture at the outgoing end of the power supply and at the remote end of the cable.
The maximum allowable length of the fieldbus segment is 1900m. Segment length = trunk length + all branch lengths. The above length is a conservative value. The branch length is 1 to 200m. Each branch can only connect one FF device. The recommended branch length is 30m.
Mainline cables, power supplies, grounding and lightning protection, and network segment risk management (level 4 valve and network/network segment) are all clearly defined. With respect to multivariable field devices, multivariable transmitters of the AI ​​function block type can only be used for one control loop, other variables are used only for monitoring, and multivariable transmitters belonging to the MAI function block are used for monitoring only.
The conceptual model of FISCO fieldbus intrinsic safety is jointly completed by the German Federal Institute of Physics and Technology and several internationally renowned manufacturers. In addition to the reference to this guide, the specific project also reads relevant standards and procedures. The purpose of proposing and developing FISCO is to provide power to the fieldbus network/network segment while ensuring that the energy level does not cause an explosion. Due to the limited DC power common to multiple field devices, the long cable and capacitor capacity stored in terminators, traditional intrinsic safety devices and interconnection rules limit the use of intrinsically safe systems. Specifically, the FIS-CO parameters of the EEXiaIIc and EExibIIC/IIB explosion-proof grades are given.
The FOUNDATION fieldbus load is determined by the minimum of the following four parameters: network segment risk management, spare capacity, network segment execution time, voltage drop, and current limit. Spare capacity should be reserved for 25% in the design of the network segment, and a control loop (ie, 1 transmitter and 1 final component) can be reserved for the specific design. The default execution time of the network segment is 1s. It is recommended that the maximum number of devices in a network segment be: the only network segment with a monitor is 12 devices; the network segment requiring a 1s execution time is 12 devices with 4 valves; the network with a required execution time of 0.5 s The segment is six devices with two valves; the network segment requiring a 0.25s execution time is three devices with one valve.
The minimum value determined by the voltage drop and current limit must be analyzed for each FF network segment. The calculated device voltage must exceed the minimum operating voltage of the equipment by 4V (that is, 9+4=13V), which will be added to the network segment in the future. Reserve margin for equipment. Another example is the current of a single factory equipment does not exceed 15mA, the output device current does not exceed 25mA, network equipment does not exceed 16, the network length does not exceed 1000m, and 16 input devices are located at the farthest end of the bus, the total current consumption is 16x15 =240mA. The impedance of the 1kml 8# loop is 44Ω/kn and the line voltage drop is 44x0.24=10.6V. The minimum voltage of the power supply is 10.6+9=19.6V.
The FF network segment also calculates the virtual communication resources VCR and names the network segments, branches, loops, and meters.
Third, the main system (host system)
The FOUNDATION fieldbus host system, host system, FF host, host computer, and system host (and host computer) have the same meanings in several terms. They all refer to the field bus network/segment connected to FFH1 (31.25kb/s). And through the HIST host interoperability testing system. The system should use standard products (standard hardware, system software and firmware), and the system software and firmware should be able to meet the specified requirements after configuration.
The HIST technical specification is FF-569, which is generally supervised by Fieldbus Foundation personnel, but it also points out that for FF host systems that do not support the specified HIST performance, after thoroughly evaluating the performance limitations of the main system, the chief project engineer and project leader should Approve its use in writing. About FF-569 is equipped with the performance and components of the FF host. The host can be a configuration tool, a recording device, an alarm display panel, a human-machine interface, or a combination of functions. These are manufacturers of automation systems other than DCS or large-scale system integrators. The development of products matching FF creates opportunities.
To develop a set of operational test procedures, FF-569 defines a common set of FF host performance metrics that can implement some or all of the performance within the host. These properties include: device tag assignment, device address assignment, configuration of fully-connected master devices, block tag configuration, block instantiation, standard blocks, enhancement blocks, client blocks, function block link configuration, FF alert groups Status, FF alarm processing, FF trend configuration, FF trend processing, device description (DD) service, DD method execution, DD menu processing, DD edit display processing, capability file, etc. In addition, the performance of downloading upgrade software to field devices through the host online will become a host test requirement in the near future.
It also stipulates to the standard products that the information from the FF equipment shall not be mapped into the system by the I/O channel method. When the control strategy is implemented, the functional blocks residing in the equipment may be used directly.
Provisions for spare capacity and expansion of the host system are specified: When configuring the system for all components, at least 10% of spare capacity is reserved for each system. This includes application software, graphics, history, reports, and trends. In the basic system, 10% spare capacity is reserved for various types of I/O. It is recommended to reserve 10% to 50% of the space for the backplane and marshalling terminals. The module reserves 20% to 25% spare capacity. The communication network inside the automation system should reserve 10% of the node address. When a new device is connected to the control network, the communication network can use the network self-addressing technology (plug and play) to assign a unique new controller address automatically. . Each H1 module can have at least two network segments, and each network segment can have at least 16 FF devices.
As a main system, DCS currently used should support the FOUNDATION fieldbus function, that is, the DCS main system function should be able to integrate with the FOUNDATION fieldbus as follows: automatic node addressing; interoperability; use of standard DDL (equipment Description language) Direct configuration of the device; direct integration of FF device operation, maintenance and diagnostics data; adjustment of parameters, modes, alarms and data quality; no commissioning and start-up delays, should be available to existing networks/segments (eg equipment bits New field devices are added in number/placeholder) and all configurations can be performed; without shutting down the network, the configuration of field devices can be realized while the main system is running; a device capability file should be provided.
The main system data transfer function should be able to integrate third-party database systems into fieldbus devices. If you use OPC (OLE for process control), you should ensure that the product passes the "OPC Compatibility Test".
The main system as a configuration tool should provide online and offline configuration tools. The configuration tool should have multi-user and multi-instance capabilities. Requirements for system integration capabilities: All master FF functions, including engineering, configuration, maintenance, and operational display capabilities, should be integrated into a single, seamless main system. Engineering, configuration, maintenance and operational performance should be compatible and seamlessly integrated with conventional analog or discrete I/O, smart HART and dedicated I/O, bus-based I/O and FF systems, and it is recommended that: Do not use only Independent software tools, displays, or programs that target FF and are incompatible with legacy systems. In terms of method and appearance, the main FF configuration should be consistent with the traditional configuration. When the FF function is mapped to a dedicated function block, the internal mirroring or shaded function blocks used by the control system should be completely transparent to the configuration engineer, technical maintenance personnel, and operators. Both configuration and operation should use single, unique and independent function blocks and parameter tag names. Using the same configuration tools, both FF and traditional control strategies are able to save, restore, and partially download the main control system database in a seamless and transparent manner. All these reflect the fact that the Fieldbus Foundation has fully considered the inheritance and inclusiveness of the automation system, protecting the interests of end users, protecting the interests of existing automation equipment manufacturers, and facilitating the integration of new FF products into the automation market. Accepted by the majority of users, this is the trend of PAS development in the process industry automation system for a long time to come.
Off-line FF configuration refers to the FF policy configuration when the network/segment or FF device is not connected. The host can configure all the FF function blocks and parameters and support the technical specifications of the DD service and Common File Format (CFF). Regarding the transparent management macro cycle scheduling, the minimum non-scheduled non-cyclical time is maintained, and at least 70% of the unscheduled non-cyclical time is reserved for the first installation.
There are several aspects of host system redundancy and stability, troubleshooting, maintenance and diagnostics, advanced diagnostics, and computer-based maintenance and evaluation criteria.
Fourth, the software configuration Configuration (Configuration) the definition of the term is: In order to meet the system requirements, the physical installation of the hardware module; or to meet the system requirements of the software option settings. The guide also pointed out that the so-called "configurable" meaning is the ability to select and connect standard hardware modules to create systems; or to modify or change the capabilities of software functions by modifying parameters without modifying or updating the software. These definitions serve as an opening for this section and are very helpful for everyone to understand the importance of software configuration.
During the configuration process, the control system graphics and FF-related graphics should meet the existing standards for end-user graphics and provide a wealth of additional instructions (including device status alarms, FF trends, and alerts).
The FOUNDATION fieldbus node address is the network segment describing the current address of the device. The node address range is 0~255. The allocation is as follows: 0 ~ 15 reserved; 16 ~ 247 is the address used by permanent equipment, the general low number for the upper communication and host interface, some of the high number assigned to online field devices (to improve efficiency, the range is usually reduced); 248 to 251 are addresses for non-permanent devices, such as new or deactivated devices; 252 to 255 are addresses for temporary devices, such as handheld tools.
In addition, device naming, control strategy/module naming, and FOUNDATION fieldbus block naming are stipulated. These are indicated on the P&ID, in which the suffixes and named instances of multiple identical blocks in a device are shown in Figure 3, where In the device TT temperature transmitter 1000, there are two analog input signals respectively labeled with AI_l and Al_2.
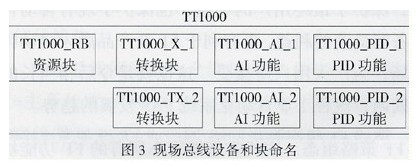
Regarding localization of the control function, the module is named according to the bit number indicated by P&ID. As shown in FIG. 4 , the control block can be implemented in a field device or a main controller. For field-based control, equipment with PID control algorithms should be marked on the corresponding network/network segment drawings and include the bold letter P. For single-loop PID control in field devices, all the functional blocks that make up the control loop are Should reside on the same network segment (usually the PID is placed in the control valve positioner); if it cannot reside on the same network segment, the PID control algorithm can be placed in the main system (such as a DCS control station). For cascade control, the preferred configuration is the positioning of each cascaded loop function block and device on the same network/segment. The primary PID controller should reside in the primary measurement transmitter and the secondary PID control should be Stay in the final component; in another case of cascade control, the primary PID controller resides in the central controller/host, the secondary loop functional block and device reside on the same network segment, and the secondary PID control can reside in the final Components.

When deciding the PID position, execution time, advanced diagnostics, failure modes, and operator access need to be considered. As with conventional control systems, it is also necessary to determine the correct behavior of each control loop fault protection when the loop and equipment failure modes.
Each configuration option and default value should be documented as a guide to the control strategy and reviewed and approved by the end-user engineering representative as it constitutes the configuration basis for the behavior of the equipment and control system under "abnormal" conditions, which is a safety measure for the plant. And reliable operation is very important. The guideline document should highlight the differences between the configuration and operation of FF and non-FF control strategies, and also include configuration options and default values ​​for the main system including the settings, equipment, and asset management software.
The guide documentation should provide descriptions of various typical function blocks and control modules, describe in detail the settings of parameters and the operation of subsequent blocks/modules. The contents of the narrative discussion include parameter configuration, operation of the signal "state", determination of invalid values, and failures. Mode switching, initialization performance, limit performance to prevent reset, etc. Some examples of default settings for instance loops are as follows:
(1) For an invalid PV (process variable), the loop mode should be switched to the manual mode. This state generates an alarm and displays it on the graph. The panel color changes and the data display disappears.
(2) Loop mode should ignore the suspicious PV. This state will not cause an alarm, but it will be displayed on the graph and the panel color will change.
Regarding alarms and warnings, the fieldbus includes 15 alarm priorities and is mapped to the main system. For example, in the DCS, there are no actions (level 1), logs (levels 2 to 4), and low levels (levels 5 to 7). High (8-11), emergency (12-15). The host must support the time synchronization and alarm time stamping of field devices.
Communication errors, misoperations (diagnoses) or malfunctions, on-site equipment will generate warnings. Warnings are the collective name for alarms and events. The alarm is generated and eventually cleared (disappeared), two reports are generated, and only one report occurs. The FF system uses alerts to notify the user of the various states of the device.
The FOUNDATION fieldbus is able to capture the trend of the most recent 165 process variables and status points and provide time stamps for each network/network segment.
Regarding network communication and scheduling, FFHl's data link layer LAS link activator is responsible for the coordination of all communication on the fieldbus, completes token transmission control, and guarantees data transmission services and link time synchronization services, generally in the main control system redundancy. H1 network interface plug-in, its network / network segment execution time, macro cycle, network / network segment scheduling should leave a margin, to ensure that there are enough non-scheduled time in each cycle to transfer non-cyclical (maintenance and configuration) information .
The failure rate of the PID block must be set to a minimum of 3 to ensure that the setpoint tracking action is performed.
Regarding VCR virtual communication relations, or virtual communication resources, when configuring a complex control strategy, it is necessary to pay attention to the number of functional blocks and VCRs supported by field devices and main systems. Under normal circumstances, field devices cannot support more functional blocks and the number of VCRs, so the complex control strategy should be more placed in the main controller (such as DCS control station). In order to clearly see the example shown in Figure 5, first make the following description: The FOUNDATION fieldbus communication model is divided into four levels, namely, the physical layer, data link layer, application layer and user layer, but according to the function has 3 The part, that is, the communication entity, the system management kernel, and the functional block application process, each part communicates information through the VCR, so the virtual communication relationship is the configuration application layer channel and can provide data transmission for the application program. The FOUNDATION fieldbus describes three types of VCR virtual communication relationships: publisher/subscriber, guest/server, and source/receiver. The VCR is included in the Network Management Information Base (NMIB), and the addressing of VFD virtual field device objects is implicitly defined by the VCR in the virtual communication relationship list.
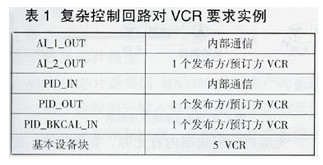
In the system engineering guide, it is also required that the host system configuration tool and data should have import/export functions for all function blocks and module data. The formats include: comma separator, Microsoft Excel, text, Microsoft Access, and SQL. The host should be able to download all the function blocks using the imported data. Download features include control functions, scheduling and initialization, exporting and updating external databases. For the operator display, it is required to achieve process visualization, high confidence, safety, ease of use, high utilization, easy maintenance and management, and no need to stop the production process when the software version is upgraded. It also puts forward a series of strict requirements for system management, control and data processing, system configuration tools, and display.
In the face of FF entering the engineering practice stage, China should take the enterprise as its main body, and it must combine the development of FF field instrumentation and main system as well as the work of FF registration and interoperability certification.

The introduction of ethylene engineering to digest and absorb FF application technology in the system engineering guide, also requires the host system configuration tools and data should have all function block and module data import/export capabilities, its format includes: comma separator, MicrosoftExcel, text Microsoft Access, SQL. The host should be able to download all the function blocks using the imported data. Download features include control functions, scheduling and initialization, exporting and updating external databases. For the operator display, it is required to achieve process visualization, high confidence, safety, ease of use, high utilization, easy maintenance and management, and no need to stop the production process when the software version is upgraded. It also puts forward a series of strict requirements for system management, control and data processing, system configuration tools, and display.
In the face of FF entering the engineering practice stage, China should take the enterprise as the main body, and in addition to the FT field instrument and main system research and FF registration and interoperability certification work, we must combine the introduction of ethylene engineering to absorb and popularize FF application technology. Make it play a role in actual process industrial production as soon as possible.
The extruder machine has single screw machine and twin screw machine. A variety of puffed food snacks can be produced by adjusting the Dies.
we are specialized manufacturers with 15 years of extruder experience, we have the perfect after-sales service and technical support. Look forward to your cooperation!
Twin Screw Extruder,Double Extrusion Machine,Single Screw Extruder, Screw Extruder
Jinan Chenyang Technology Co., Ltd. , https://www.cybabyfoodprocessingline.com