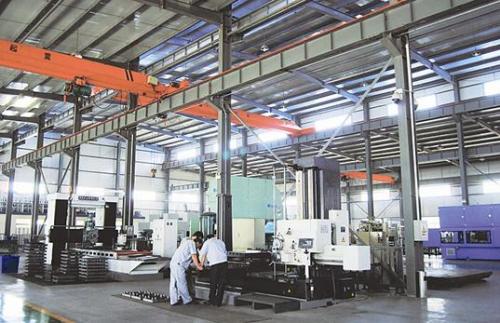
In recent years, Wuhan cylinder manufacturers have performed well in the basic components of hydraulic cylinders and have continuously developed new products.
The hydraulic cylinder component manufacturing and manufacturing base of Wuhan oil tank manufacturer takes the hydraulic cylinder as the main part of the project construction and builds a high-end hydraulic park project. The project will rely on Yuci’s advantages in hydraulic products, technology, talents and brand sales, and focus on the development of high-pressure plunger pumps, high-performance hydraulic valves, high-performance vane pumps, high-performance gear pumps, and high performance on the basis of the original products. Cylinder, high-performance hydraulic system six categories of high-end hydraulic products. We have meticulously created "one park (world-class, first-in-class hydraulic industrial autonomy industrial park), two centers (developing national-level technology centers, establishing national-level hydraulic product experimental testing centers, and four bases). , the largest electromechanical and hydraulic integrated hydraulic component manufacturing base; second, the largest and most advanced hydraulic system and device manufacturing base in China; the third is the high-pressure precision casting production base; and the fourth is the export-oriented hydraulic product export base). To improve the level of equipment manufacturing, in order to change the long-term dependence on imports of high-end hydraulic products in China, to make new contributions to the nationalization of China's major equipment.
In addition, the low-pressure rotor of the 330,000-kilowatt steam turbine developed and produced by Wuhan oil cylinder manufacturers is another latest technological innovation in the field of forging by Wuhan oil tank manufacturers after the successful forging of a 300,000-kw generator rotor. The forging weight of this product is 111.12 tons. Compared with the previous 300,000-kilowatt generator rotor, this product has higher requirements on the process, density and pressing effect, due to the vacuum carbon used for the first time in the forging process of extra large steel ingots. The new deoxidation process ensures the purity of the forgings. In addition, the cross-sectional area of ​​the low-pressure rotor is 30% to 35% larger than the rotor cross-sectional area of ​​the motor of the same class, which allows the equipment to effectively use the low-pressure steam during the actual operation, which reflects the environmental protection effect.
The die casting process involves the use of a furnace, metal, die casting machine, and die.
The metal, typically a non-ferrous alloy such as aluminium or zinc, is melted in the furnace and then injected into the dies in the die casting machine. After the molten metal is injected into the dies, it rapidly cools and solidifies into the final part, called the casting parts.
The castings that are created in this process can vary greatly in size and weight, ranging from a couple of ounces to 100 pounds. One common application of die-cast parts are housings - thin-walled enclosures, often requiring many ribs and bosses on the interior.
Metal housings for a variety of appliances and equipment are often die cast.
Several automobile components are also manufactured using die casting, including pistons, cylinder heads, and engine blocks. Most home appliances also need lightweight and
Drum Support,Drum Spider,Washing Machine Tripod,Washing Machine Support
Ningbo Sunlee Electrical Technology Co. , Ltd. , https://www.sunleeelectric.com