Multitec® sprayable polyurethane systems have proven their value in full-featured, high productivity and environmental compatibility
The Multitec® polyurethane spray system developed by Leverkusen – Bayer MaterialScience is a typical example of economic and ecological development that are not mutually antagonistic but joint development. This liquid system – with or without glass fiber reinforcement – ​​can be sprayed in open or closed molds to create parts with different geometries. This process has proven to be very effective for producing molded articles. Compared to conventional production using manual lamination, the system has a short curing time that varies between 3 and 5 minutes and has a very positive impact on productivity. In addition, the system eliminates styrene and past energy-intensive post-cure processes. Depending on the application under discussion, the manufacturer can perform multiple spray operations in succession, whether or not glass fiber reinforcement is used, to increase the strength or produce a coatable surface.
Many different types of development have long used these advantages. For example, the complex shape molded hood made by Multitec® reinforced ABS has been designed for use on new tractors manufactured by Pronar Sp. z oo (a manufacturer of agricultural machinery in Narew, Poland). Dr. Marc Schütze, an expert in Bayer MaterialScience Polyurethane Spray Systems, said: "This example is a good example of how polyurethane spray systems can also be used in the manufacture of high quality parts for commercial vehicles."
A glass-reinforced Multitec® staple fiber spray system is also used on Neoplan vehicles to produce 130 x 95 cm anti-drilling molded parts. The molded part is light in weight and can reliably protect the upper oil pan to prevent scattered debris and rotating particles.
The Multitec® staple fiber spray system also proves its value in the production of bathtubs. The shape of the bathtub is generally made by thermoforming polymethyl methacrylate (PMMA) or ABS thermoplastic film. To ensure that the molded article has the necessary stability, the back side of the thermoformed film must be reinforced. Until now, it has been mainly done by a manual process of laminating a film using unsaturated polyester and chopped fiber, which is time consuming and energy consuming. “Our polyurethane spray system is ideally suited to replace previous processes. It cures quickly, does not use styrene and adheres very well to film substrates. Currently in addition to the glass fiber reinforced Multitec® system, we are still developing a A new type of foaming system."
About BaySystems®:
Since March 1, 2007, Bayer MaterialScience has consolidated its entire global polyurethane systems business under the BaySystems® main brand. The move will have an impact on existing product brands in this area, including Baydur®, and the global network of polyurethane systems companies. More information about BaySystems® can be found at
About Bayer MaterialScience :
Bayer MaterialScience is one of the world's largest polymer producers with 2006 sales of €10.16 billion (except HC Stark and Wolff Walsrode). Bayer MaterialScience's main business areas are the production of high-tech polymer materials and the development of innovative solutions for many common products in everyday life. Its main consumers come from the automotive, electrical engineering / electronics, construction, sports and leisure sectors. As of the end of 2006, Bayer MaterialScience has approximately 30 production sites worldwide with more than 14,900 employees. Bayer MaterialScience is part of the Bayer Group.
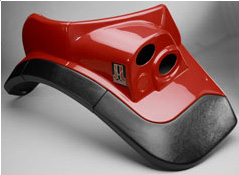
This tractor-molded hood from the agricultural machinery manufacturer Pronar in Narew, Poland, is a good example of Bayer MaterialScience's polyurethane spray system that can also be used in the manufacture of high quality parts for commercial vehicles.
Various Baypreg® polyurethane spray systems achieve a new breakthrough in composite design with lightweight, high-rigidity molded parts
Leverkusen – A composite sandwich component made from Bayer MaterialScience's proprietary Baypreg® polyurethane system is highly rigid and has proven to be of great value in a range of applications. This sandwich component is lightweight, shock resistant and rigid. Skiers and snowboards benefit from the rigid and flexible design of their sports equipment, which allows skiers to move and jump freely.
“It is this sandwich design that makes it possible,†explains Dr. Marc Schütze, specialist in polyurethane spray systems at Bayer MaterialScience. Many major manufacturers of high-strength molded parts believe that Baypreg® is a product that can truly replace traditional epoxy resins. It is not only difficult to dissolve, but also resistant to styrene, and is suitable for all molding processes and is compatible with a wide range of core materials, such as Honeycomb or plastic and paper honeycomb structure. In addition, Baypreg® can be processed with a range of reinforcing fiber materials, including glass, cardboard or natural fibers. This spray system ensures that these materials are fully wetted and saturated.
As a resin for sandwich design, it will all be used to create an optimized blend of various materials that is ideal for the production of skis and snowboards. The high integration of polyurethane means that it can be mixed with decorative surface materials.
The Baypreg® system with built-in release agent can be used for molded parts without decorative layers, such as the pedals for motorhomes and caravans. Here, the composite sandwich component is made by using the spray system, which has similar characteristics to the winter sports equipment: light weight, strong shock resistance, high rigidity and high quality surface. Examples of applications in this field include the double pedals produced by the French car parts manufacturer Rapido camping car by Formtec PUR Verarbeitungs GmbH in Dornstetten, Germany. Polyurethane expert Schütze explains: “This sandwich composite consists of an unfolded polyurethane core and two outer layers of natural fibers. The natural fiber material is saturated in a black liquid system and placed in an open mold. Place the core layer and another layer of impregnated fiber. Close the mold and the part will be automatically pressed into the desired shape." The polyurethane reacts in just a few minutes, creating a strong permanent bond between all parts.
Glass fiber reinforced polyurethane for greater safety:
High impact protection cover for ski sleds
Plastic materials operating at low temperatures must meet the high demands of mechanical properties, as many materials quickly become brittle and fragile below freezing. Sleds travel in the suburbs, and when they leave the preset track, they often collide with objects such as branches or lightly; in low temperature conditions, if the car body material is not suitable for operation, such minor accidents may result in expensive maintenance costs.
The protective cover on Bombardier-Nordtrac's skis is strong enough to withstand these harsh environmental conditions.
Bayflex® 180 molded products, approximately 1.10 meters long, 1 meter wide and 0.4 meters high, provide outstanding impact strength over a wide temperature range, while the consolidation of natural mineral fibers gives them excellent inherent hardness.
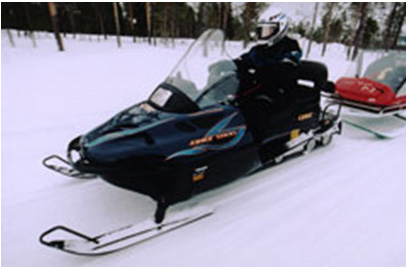
Bombardier-Nordtrac OY of Rovaniemi, Finland, is assembling a protective cover made of Bayer Material & Bayflex® 180 mineral fiber reinforced R-RIM polyurethane on its new ski. The selection of this material to manufacture large-area parts is mainly based on the high impact strength of the material under low temperature conditions and a short production cycle.
Widely applicable to the aerospace industry, railway transportation, automotive engineering, electrical/electronics industry and mechanical engineering Leverkusen – Bayer MaterialScience's polyurethane resin system Blendur® is ideal for high temperature applications and is used in each The production of high-strength thermoset composite materials is widely used in the aviation industry, railway transportation, automotive engineering, electrical/electronics industry and mechanical engineering.
Harald Rasselnberg, a polyurethane specialist at Bayer MaterialScience, commented: “Resin materials can be used in high temperature environments at 250 ° C and can withstand higher temperatures in a short period of time.†The inherent flame retardancy and high temperature rating of resin materials means H The material is suitable for a wide range of applications such as fiber reinforced structural members, insulator and switching technology, electrical and electronic component casting, and can be used as a shielding material for hot press molding. Rasselnberg went on to say: “The high temperature resistance of Blendur® enables it to be used in these areas and can replace standard epoxy resins and phenolic resins.â€
Because this material consists of a special polyurethane and epoxy component, it can be processed using all existing thermosetting plastic manufacturing techniques, including resin transfer molding (RTM) and pultrusion dies, making it more widely used. . The series currently on sale includes a resin system that constitutes a compatible and mixed grade of the system with a viscosity in the range of 30 to 2,500 mPa. The selection of a suitable catalyst as the "second component" enables the service life to be set within a time period of 10 minutes to 6 hours.
This product is supplied in a liquid state and is first brought to an intermediate state by filling and reinforcing materials, such as exposure to a latent catalyst or addition of an initiator at room temperature. In this intermediate state, a high density, three-dimensional crosslink is formed. The second step is the curing process, which lasts for several hours, during which the solid, fragile material hardens into a thermally hardened plastic with high dimensional stability. Casting parts made of Blendur® have almost no “cold flow†due to centrifugal forces, which often have an effect on the quality of the plastic.
Nantong Weizhuo Environmental Protection Equipment Co.,Ltd , https://www.cwz-floorscrubber.com