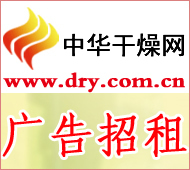
China Drying News, “12th Five-Year Plan of Ethylene Industry†proposed that by 2015, China’s total ethylene production capacity will reach 27 million tons, and the new coal will produce 4.5 million tons of olefins from methanol, making the production of coal-to-olefins account for the national ethylene More than 20% of the total production capacity; Accelerate the diversification of ethylene raw materials and reduce the excessive consumption and dependence of the ethylene industry on petroleum resources. With the breakthrough of many hydrocarbon production technologies, this plan is expected to be realized in advance. This is a prediction made by several experts when interviewed by reporters.
Methanol to Olefins: Preliminary Industrialization
In mid-December 2012, the 5,000-ton/year industrial side-line test facility built with the proprietary MTP technology independently developed by Sinopec Shanghai Petrochemical Research Institute was successfully put into production at Yangzi Petrochemical and added to China's non-oil route olefins. Industrialization technology path. This is another breakthrough in the non-oil route olefins field following the successful development of the SMTO technology for coal to olefins and the establishment of a 200,000-ton/year industrialization unit of Zhongyuan Petrochemical.
“The completion of this pilot project will completely break the pattern of foreign monopoly of MTP technology and will accelerate the industrialization of Sinopec and even China’s non-oil route olefins production technology.†said Jiang Rongxing, deputy chief engineer of Sinopec Engineering Construction Co., Ltd. (SEI). .
He said that in 2010, China’s ethylene capacity will be less than 15 million tons. To achieve the capacity target of 27 million tons in 2015, it means that 12 million tons of ethylene capacity will be added. If all are produced with naphtha, an additional 120 million tons of oil refining capacity will be needed. However, at present, China's vehicle fuel supply is increasingly tight, it is impossible to produce more oil to produce ethylene, and the development of industrial production of olefins other than oil is urgently needed. As a result, Sinopec has successively developed SMTO and fixed bed MTP technologies, and plans to start four coal-to-olefins projects in Inner Mongolia, Guizhou, Anhui and Henan during the “12th Five-Year Plan†period.
“The industrial one-step fixed-bed hydrocarbon production facility with 100-thousand-ton/year methanol built using domestic technology has been successfully put into production since March 2012. In less than a year, it has generated more than 300 million yuan for the company. Currently, The company is stepping up the construction of a 100,000-ton/year capacity expansion project and will eventually form a 500,000-ton/year methanol-to-hydrocarbon scale.†Chen Xuewei, executive deputy general manager of Inner Mongolia Qinghua Group, told reporters.
According to Chen Xuewei, its one-hundred-ten thousand tons/year methanol one-step system for hydrocarbon production, with an investment of only RMB 550 million, uses crude methanol as raw material and uses a zeolite catalyst. The light aromatics accounts for 80% of the products and the liquefied gas + heavy aromatics ≤20%. . Compared with the two-step technology of US Mobil and German Wood which have already achieved industrial application, the one-step method has the characteristics of short process flow, easy operation, small project investment, high product yield, and loose raw material requirements.
Aromatic hydrocarbons from methanol: eve of industrialization
“The production of a single olefin or aromatic product may cause investment risks due to market fluctuations, so we are working with Nankai University to develop new catalysts and reactors, and related control systems. Once successful, will produce both aromatics and olefins on one unit at the same time. At that time, the output of aromatic hydrocarbons and olefins can be flexibly adjusted according to market conditions to maximize the benefits of the company, said Chen Xuewei.
"Owing to the industrial application of methanol-based aromatics technology, it will completely end the pattern of dominating the oil route," said Wei Fei, a professor at Tsinghua University. He told reporters that Huatai Yulin's 30,000-ton/year industrialized experimental device for the production of paraxylene technology (FMTA) was developed using Tsinghua University's independently developed methanol multi-stage fluidized-bed carbonylation reaction, and it is ready for trial operation and is expected to be tested in the second quarter. run. At that time, 3 tons of methanol can produce 1 ton of aromatics (of which 80% are domestically short of p-xylene). Compared with naphtha catalytic reforming multi-stage deep-freeze crystallization to produce aromatics, FMTA technology has fewer side reactions, high catalyst selectivity, high single-pass yield of aromatics, wide source of raw materials, and low production cost.
“At present, the price of paraxylene is about 30% higher than that of olefins, and the consumption of raw materials for each unit of product is similar to methanol, indicating that methanol-based aromatics is not only more competitive than naphtha-based aromatics, but also economically superior to methanol-based olefins. Once the industrialization test is successful, it will surely speed up the diversification of aromatic hydrocarbon materials," said Wei Fei.
Coal to Acetylene: Bright Prospects
According to Jin Yong, academician of the Chinese Academy of Engineering, the rise of the acetylene industry will also accelerate the process of diversification of hydrocarbon feedstocks.
According to reports, the acetylene technology for the partial high-temperature oxidation of natural gas developed by Tsinghua University has completed a 10,000-ton/year industrial test facility; the coal-to-plasma acetylene technology jointly developed by Tsinghua University and Xinjiang Tianye Group has been built. The maximum torch power of 5 MW plasma cracking coal acetylene plant, annual acetylene production up to 4,000 tons. The device has passed continuous operation test for 72 hours, and it is planned to develop 10,000-ton plasma coal acetylene device.
“Once these two technologies are supported by policies and guaranteed by natural gas supply, they will be quickly promoted with their significant economic, environmental, and energy-saving benefits. By then, companies will only need to hydrogenate acetylene to obtain ethylene. There is no need for a large-scale refinery to build an ethylene project like it is now,†said Jin Yong.
According to the reporter’s understanding, Hebei Tianyuan Enterprise Group adopted the self-designed 10,000-ton/year methanol-based alkane (MTG) industrialized experimental device designed and built by Nankai University's catalyst and passed the appraisal in February 2012. At present, pastoral companies are spending 280 million yuan to build 100,000 tons / year MTG industrialization demonstration projects. Shanxi Jinmei Coal Group, Shanxi Haobao Group, Yunnan Xiehua Group and other units also adopted two-step or one-step process technology to build methanol-to-alkane plants.
According to rough statistics, by 2015, China's non-oil route olefins production capacity will exceed 12.5 million tons / year, non-oil route alkane production capacity will reach 700,000 tons / year, non-oil route aromatics production capacity of 1.5 million tons / year, initially formed The pattern of coexistence of oil-based hydrocarbons and multiple raw material routes. After the "Thirteenth Five-Year Plan", with the further expansion of the non-oil route, the scale of non-oil-based hydrocarbon production will be equivalent to that of the petroleum oil route, and the diversified pattern of China's hydrocarbon production will form.
The slips are standard equipment for running tubulars such as drill pipe, drill collar, and casing. Similarly, our rotary hand slips are machined, by strict quality control procedures, for use in API standard.Drill pipe slips are used to accommodate drill pipe from 2.3/8" to 5.1/2" O.D. Drill pipe slip is classified as type short(SDS), medium(SDML) and extra long(SDXL) according to gripping length. SDS slips are designed for shallow hole drilling, SDML slips are the perfect choice for all medium depth drilling, SDXL slips are designed for deep drilling. All rotary slips provided are API 7K certified
Drill Pipe Slips,Casing Slips Drilling,Drill Pipe Slips Parts,Pipe Slips
Xi'an Qinsen Technology Co.,Ltd . , https://www.xianqinsen.com