Dry mortar is one of the raw materials for high-speed railway track slab grouting. After testing and appraisal, the plate type ballastless track that is applied with dry mortar has outstanding advantages such as good stability, strong durability, even rigidity, and low maintenance. However, due to the special nature of the high-speed rail special mortar, the precision of the mixing station is extremely high. Therefore, at present, most domestic dry powder mortar mixing stations do not have the production capacity of high-speed rail special mortar. However, the import of such dry powder mortar is expensive. In this context, SANY Heavy Industry Mixing Equipment Co., Ltd., in order to meet the demand for high-speed railway construction, began researching and manufacturing the dedicated dry powder mortar mixing station for high-speed railways from February this year.
During the research and development process, the dry powder station of the agitation equipment company overcomes multiple technical difficulties, and in particular solves the world's problems in the control of dry powder mixing measurement accuracy. The ratio of trace elements in dry mortar is the key to dry powder quality. Dry powder station design, if the use of ordinary electronic scales for the measurement of trace materials, the measurement accuracy is often not meet the requirements. After repeated research, the weight loss feeder used in the overall measurement, which not only ensures the measurement accuracy, but also greatly reduces the manual workload. In addition, in the finished dry powder discharge, there is a problem of how to conveniently transport the finished dry powder material to the construction site and avoid the occurrence of segregation of the dry powder during transportation. The mixing equipment adopts an advanced ton bag packaging process, which facilitates the transportation and storage of the finished dry powder without segregation. At the same time, the mixing station features efficient dust removal and environmental protection.
Since the establishment of the project, the high-speed railway dedicated dry mortar mixing plant has achieved two sales. According to the medium and long-term development plan for China's railways, by 2020, more than 12,000 kilometers of passenger dedicated lines will be built. The customer stated that the prospects for the dedicated mortar mixing plant for the Sany High Speed ​​Rail are very promising.
Metals, alloys and composite powders commonly used in thermal spray hardfacing technology and coating service. These unique powders are instantly heated by thermal spraying (welding) methods such as high temperature flame or explosive flame, and are sprayed and deposited on the cold or hot workpiece surface with high-speed heat flow in a molten or semi-melted state to form a surface Reinforcing layer, in order to improve the wear resistance, corrosion resistance, heat resistance, oxidation resistance or repair of external dimensions of the workpiece surface. XTC produces WC, CrC, Oxide Ceramic, Boride Powder, Metal Alloy Powder, Pure Metal and Spray Wire, etc. product. For HVOF/HVAF/plasma/Flame spray coating and applications. Meet the wear and corrosion resistance requirements of different surfaces.
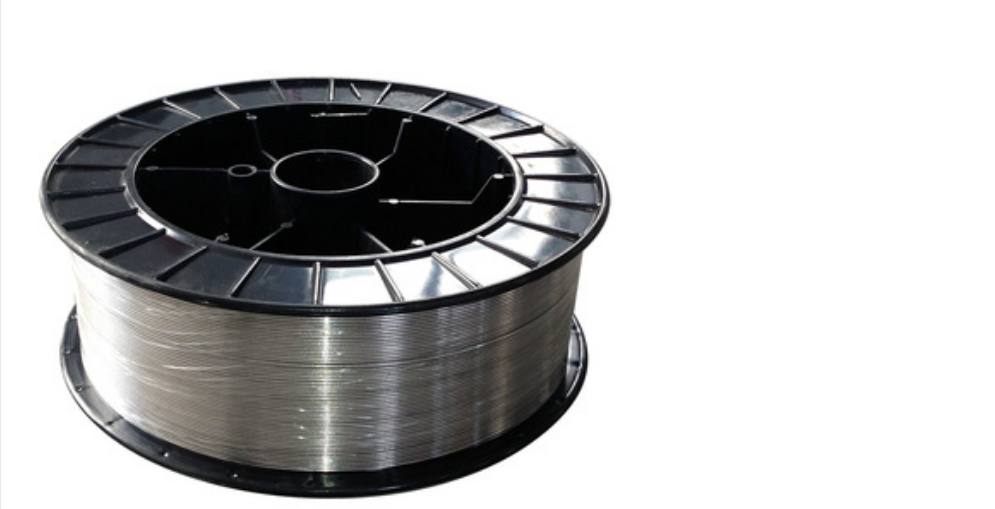
WC, CrC oxide ceramic powder and boride products are excellent in wear resistance and high temperature corrosion resistance. Taking WC products as an example, the hardness can reach HV1300-1500, and the temperature of CrC products can reach 800 degrees Celsius.
Metal alloy powder, Pure Metal and Spray Wire products have more applications in glass mold, steel and machinery industries. And XTC products are now become more and more popular in Metal spray coating and thermal spray coating industry.
Coating Service,Metal Spray Coating,Flame Spray Coating,Thermal Spray Coating
Luoyang Golden Egret Geotools Co., Ltd , https://www.hvafspray.com