The current development of the automobile manufacturing industry is characterized by intensified competition, how can we continuously improve production efficiency, reduce manufacturing costs, provide customers with high-quality products at competitive prices, and meet the ever-increasing demands of users in time, becoming enterprises in the automotive manufacturing industry The focus of common concern. Different metal machining processes have different requirements for metal machining fluids. The following is a brief introduction to the requirements of metal machining fluids by several major machining methods in the automotive industry.
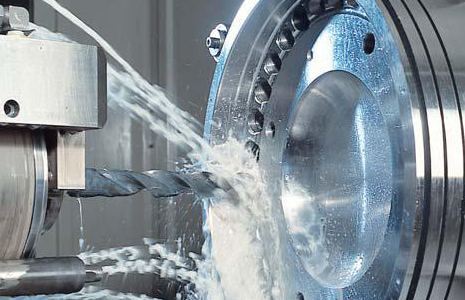
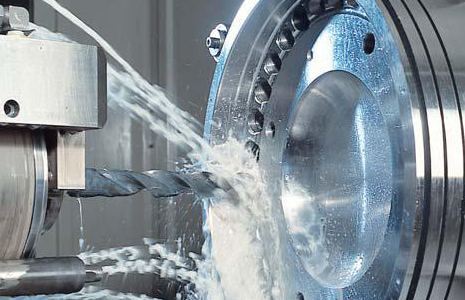
1, turning and milling
For the machining of steel and cast iron materials in general, their processing methods generally have higher cutting speeds, generate more heat, and require sufficient cooling. Emulsification and semi-synthetic metalworking fluids can be used.
2, drilling and reaming
These two processing methods have relatively high requirements for the lubricating and cooling performance of metalworking fluids. Generally, the semi-synthetic metalworking fluid containing the extreme pressure additive type with better lubricating properties should be selected to ensure not only its lubricating performance but also good cooling. performance.
3, grinding
Grinding speed is faster, requiring higher cooling and lubricating performance for metalworking fluids. In the grinding process, the friction between the abrasive and the surface of the workpiece must be reduced in the contact area, thereby reducing the temperature on the grinding surface. This requires metalworking fluids to provide good lubricating properties, and accompanied by a gentle flow of high-volume metal processing to remove heat to meet Capricorn's processing accuracy requirements. The selection of metalworking fluids for grinding processes is relatively complex and considers a number of factors such as workpiece materials, grinding wheel materials, grinding methods, cutting parameters, and the like.
The above kinds are just a brief introduction of the selection of several different student number processing methods for metalworking fluids, and only take into account the more important factors, in fact, the selection of metalworking fluids also need to consider other relevant factors, such as: metal Type of machining, metal parts of the workpiece, material and type of tooling, recommendation of the equipment manufacturer, comprehensive cost considerations (including initial costs and maintenance), environmental factors (including safety factors, personnel health factors, etc.)
In the automotive manufacturing industry such as engine and gearbox machining, a CNC machining center can include several machining methods. Since various machining methods do not show exactly the same metal processing fluid, when selecting metal machining fluid performance, first It should be considered that the metalworking fluid must be able to meet the requirements of the most difficult processing methods on the human processing performance, and then consider the need for other processing methods on the metal processing fluid to select the appropriate metalworking fluid.
We have got 220kV Transmission Line Steel Pole Quality Certificate from Power Industry Steel Tower Qualified Inspection & Test Center from 2001 year.
Our steel poles are made from quality sheet through bending, forming, automatic welding and hot galvanization. We can reach one-run machining length of 14m and can bend sheet of thickness up to 45mm. We adopt advanced welding procedures, automatically weld main joints and reach rank-II welding quality. We supply more than 4000ton Substation Structure for our clients every year.
High Voltage Transmission Line
Transmission Line Steel Pole, Utility Pole, Steel Tubular Pole, High Voltage Transmission Line
Jiangsu Xinjinlei Steel Industry Co., Ltd. , https://www.steel-pole.com