Ultrasonic sensors are sensors developed using the characteristics of ultrasound . Ultrasound is a kind of mechanical wave whose vibration frequency is higher than that of sound waves . It is generated by transducers vibrating under the excitation of voltage. It has high frequency, short wavelength, and small diffraction phenomenon, especially good directionality, which can become ray and orientation. Dissemination and other characteristics. Ultrasonic penetration of liquids, solids is very large, especially in the sun opaque solid, it can penetrate depths of tens of meters. Ultrasonic waves that encounter impurities or interfaces can produce significant reflections and reflect back into echoes, and Doppler effects can occur when moving objects are encountered . Sensors developed based on ultrasonic characteristics are called "ultrasonic sensors" and are widely used in industry, defense, and biomedical fields.
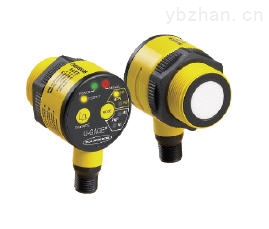
Ultrasonic probes are mainly composed of piezoelectric wafers that can emit both ultrasonic and ultrasonic waves. Low-power ultrasound probes are used for detection. It has many different configurations and can be divided into straight probes (longitudinal waves), oblique probes (transverse waves), surface wave probes (surface waves), lamb wave probes (lamb waves), dual probes (one probe emission, one probe reception) Wait.
The core of the ultrasound probe is a pressure in its plastic jacket or metal jacket.
Ultrasonic sensor
Chips. There are many types of materials that make up the wafer. Wafer size, such as diameter and thickness, are also different, so the performance of each probe is different, we must understand its performance in advance before use. The main performance indicators of ultrasonic sensors include:
working frequencyThe operating frequency is the resonant frequency of the piezoelectric wafer. When the frequency of the AC voltage applied to both ends is equal to the resonance frequency of the wafer, the output energy is maximum and the sensitivity is the highest.
Operating temperatureBecause the Curie point of the piezoelectric material is generally high, especially for the use of diagnostic ultrasound probes
Ultrasonic sensor
The power is small, so the operating temperature is relatively low, and it can work for a long time without failure. Ultrasound probes for medical use have relatively high temperatures and require separate refrigeration equipment.
SensitivityIt mainly depends on the wafer itself. The electromechanical coupling coefficient is large and the sensitivity is high; otherwise, the sensitivity is low.
DirectivityUltrasound sensor detection range
Ultrasonic sensing technology is used in different aspects of production practices, while medical applications are
Ultrasonic sensor
One of the most important applications is the use of ultrasound as an example to illustrate the application of ultrasonic sensing technology. The application of ultrasound in medicine is mainly to diagnose diseases. It has become an indispensable diagnostic method in clinical medicine. The advantages of ultrasonic diagnosis are: no pain, no damage to the subject, simple method, clear imaging, and high diagnostic accuracy. Therefore, it is easy to promote and is welcomed by medical workers and patients. Ultrasound diagnosis can be based on different medical principles. Let's take a look at one of the so-called A-type methods. This method uses ultrasonic reflections. When ultrasonic waves are propagated in human tissues, two layers of media with different acoustic impedances are encountered, and reflection echoes are generated at this interface. Each time a reflective surface is encountered, the echo is displayed on the oscilloscope's screen, and the difference in impedance between the two interfaces also determines the amplitude of the echo.
In industry, the typical application of ultrasonic is two kinds of non-destructive testing of metal and ultrasonic thickness measurement. In the past, many technologies have been hindered by the inability to detect the inside of an object's tissue. The emergence of ultrasonic sensing technology has changed this situation. Of course, more ultrasonic sensors are fixedly installed on different devices and “quietly†detect the signals that people need. In future applications, ultrasonics will be combined with information technology and new material technologies, and more intelligent, high-sensitivity ultrasonic sensors will emerge.
Ultrasonic distance sensor technology application
Ultrasonic penetration of liquids, solids is very large, especially in the opaque solid, it can penetrate depths of tens of meters.
Ultrasonic waves that encounter impurities or interfaces can produce significant reflections and reflect back into echoes, and Doppler effects can occur when moving objects are encountered. Therefore, ultrasonic testing is widely used in industrial, national defense, and biomedical fields.
Ultrasonic distance sensors can be widely used in level (liquid level) monitoring, robot collision avoidance, various ultrasonic proximity switches, and anti-theft alarms and other related fields, reliable, easy installation, waterproof type, small angle of radiation, high sensitivity, It is convenient to connect with industrial display instruments, and also provides probes with larger angles of transmission.
applicationAn ultrasonic sensor can detect the status of the container. When the ultrasonic sensor is installed at the top of a plastic melt tank or a plastic pellet chamber, when the sound waves are generated inside the container, the status of the container can be analyzed accordingly, such as full, empty or half full.
Second, ultrasonic sensors can be used to detect transparent objects, liquids, any surface roughness, smooth, light dense materials and irregular objects. It does not apply to outdoor, hot environments or pressure tanks and foam objects.
Third, ultrasonic sensors can be used in food processing plants to implement closed-loop control systems for plastic packaging inspections. With new technologies, detection can be performed on wet rings such as bottle washers, noise environments, and extreme temperature changes. [1]
4. Ultrasonic sensors can be used to detect liquid level, detect transparent objects and materials, control tension and measure distance, mainly for packaging, bottle making, materials handling, coal processing, plastics processing, and automotive industries. Ultrasonic sensors can be used for process monitoring to improve product quality, detect defects, determine presence and absence, and other aspects.
Ultrasonic sensor technology prevents pedaling
Nissan Motors has developed a function to prevent the vehicle from accelerating by accidentally stepping on the accelerator when the brakes are applied. When using a camera and an ultrasonic sensor to infer “when parking in the parking lotâ€, the driver will step on the throttle. Forced brakes. The technology is scheduled to be practical in 2 to 3 years. Ultrasonic sensor technology was developed to prevent accidental braking and throttle-caused accidents while parking in the parking lot.
The technology is implemented by using four cameras, one front bumper, one rear bumper and four rear bumpers each equipped with four ultrasonic sensors. The four cameras follow the "viewfinder" camera that displays the overhead image around the vehicle. Using the camera to identify white lines, etc. to infer that the car is located in the parking lot, the distance between the car and the surrounding obstacles is measured using an ultrasonic sensor to determine the timing of braking.
Prevent accidents caused by wrong brakes and throttles in two steps. When the driver wants to stop at the parking lot, if he steps on the accelerator, the speed is first reduced to a creep speed, and the dashboard icon is used to indicate the danger and an alarm sounds. If the driver still continues to step on the accelerator and is about to hit an object such as a wall, the brake is forcibly applied. The brake timing is to ensure that the car can stop when it is about 20-30cm away from the obstacle. [2]
People can hear the sound is caused by the vibration of the object, its frequency in the range of 20HZ-20KHZ, more than 20KHZ called ultrasound, less than 20HZ called infrasound. The commonly used ultrasonic frequency is several tens of KHZ-tens of MHZ.
Ultrasound is a mechanical oscillation in an elastic medium and has two forms: lateral oscillation (transverse wave) and longitudinal oscillation (longitudinal wave). Applications in the industry mainly use longitudinal oscillations. Ultrasound can propagate in gases, liquids, and solids, with different propagation speeds. In addition, it also has refraction and reflection phenomena, and there is attenuation in the propagation process. Ultrasonic waves are propagated in the air with a low frequency, typically several tens of KHZ, while in solids and liquids the frequency is higher. It attenuates faster in the air, but it spreads in liquids and solids, with less attenuation and longer propagation. Utilizing the characteristics of ultrasonic waves, it can be made into various kinds of ultrasonic sensors, equipped with different circuits, made various kinds of ultrasonic measuring instruments and devices, and has been widely used in communication, medical appliances and other aspects.
The main materials of ultrasonic sensors include piezoelectric crystals (electrostrictive) and nickel-iron-aluminum alloys (magnetostrictive). Electrostrictive materials include lead zirconate titanate (PZT). An ultrasonic sensor composed of a piezoelectric crystal is a reversible sensor, which can convert electrical energy into mechanical oscillation and generate ultrasonic waves. At the same time, when it receives ultrasonic waves, it can also be converted into electrical energy, so it can be divided into transmitters or receivers. Some ultrasonic sensors both send and receive. Here only a small ultrasonic sensor is introduced. The transmission and reception are slightly different. It is suitable for propagation in the air. The operating frequency is generally 23-25 ​​KHZ and 40-45 KHZ. This type of sensor is suitable for ranging, remote
Ultrasonic sensor
Control, anti-theft and other purposes. This species includes T/R-40-60, T/R-40-12, etc. (where T represents transmission, R represents reception, 40 represents frequency 40 KHz, and 16 and 12 represent outside diameter dimensions in millimeters). Another type of sealed ultrasonic sensor (MA40EI type). It is characterized by a waterproof effect (but not in water) and can be used as a material level and proximity switch, and its performance is good. There are three basic types of ultrasonic applications, transmissive type for remote control, burglar alarm, automatic door, proximity switch, etc.; separate reflective type for distance measurement, liquid level or material level; reflective type for material inspection, thickness measurement, etc. .
It consists of sending sensor (or wave transmitter), receiving sensor (or wave receiver), control part and power supply part. The transmitter sensor is composed of a transmitter and a ceramic transducer with a diameter of about 15mm. The transducer functions to convert the electrical vibration energy of the ceramic transducer into super-energy and radiate it to the air; and the receiving transducer consists of a ceramic transducer. Comprising an amplifying circuit, the transducer receives mechanical waves and converts it into electrical energy, which is used as the output of the sensor receiver to detect the transmitted signal. In actual use, the ceramic transducer used as a transmitting sensor can also be used. Used as a ceramic resonator of a receiver sensor company. The control part mainly controls the pulse chain frequency, duty cycle, sparse modulation and counting and detection distance sent by the transmitter.
Work programIf a high-frequency voltage of 40 kHz is applied to the piezoelectric ceramic chip (bicrystal oscillator) having a resonant frequency of 40 kHz in the transmitting sensor, the piezoelectric ceramic chip stretches and shortens according to the polarity of the applied high-frequency voltage, and then the ultrasonic wave of 40 kHz frequency is transmitted. The ultrasonic waves are transmitted in a sparse form (the degree of density can be modulated by the control circuit) and transmitted to the wave receiver. The receiver is based on the piezoelectric effect of the pressure sensor. That is, when a pressure is applied to the piezoelectric element, the piezoelectric element is strained, and then a 40KHz sine with a "+" pole on one side and a "-" pole on the other side is generated. Voltage. Since the high-frequency voltage has a small amplitude, amplification must be performed. Ultrasonic sensors allow the driver to safely reverse his vehicle. The principle is to detect any obstacles on or near the reverse path and issue warnings in time. The designed detection system can provide both audible and visual auditory and visual warnings. The warning indicates that the distance and direction of obstacles in the blind zone have been detected. In this way, in a narrow place, whether it is parking or driving, with the reverse obstacle alarm detection system, the driver's psychological pressure will be reduced, and they can easily take necessary actions.
Operating modeUltrasonic sensors use acoustic media to perform non-contact, wear-free detection of the object under test. Ultrasonic sensors can detect transparent or colored objects, metallic or non-metallic objects, solids, liquids, and powdered substances. Its detection performance is hardly affected by any environmental conditions, including soot and rain.
Detection mode
Ultrasonic sensors mainly use direct reflection detection mode. The detected object in front of the sensor causes the sensor to detect the detected object by partially transmitting the emitted acoustic wave back to the sensor's receiver.
There are also some ultrasonic sensors that use a radiation detection mode. An on-board ultrasonic sensor consists of a transmitter and a receiver, which are constantly "listening" between them. The detected object located between the receiver and the transmitter will block the receiver from receiving the emitted acoustic wave, so that the sensor will generate a switching signal.
examination range
The detection range of an ultrasonic sensor depends on the wavelength and frequency it uses. The longer the wavelength,
Ultrasonic sensor
The smaller the frequency, the greater the detection distance. For example, the detection range of a compact sensor with a millimeter-level wavelength is 300-500 mm, and the detection range of a sensor with a wavelength greater than 5 mm can reach 8 m. Some sensors have a narrow 6o acoustic emission angle and are therefore more suitable for accurately detecting relatively small objects. Other sensors with acoustic emission angles from 12o to 15o can detect objects with large tilt angles. In addition, we have an external probe type ultrasonic sensor, and the corresponding electronic circuit is located inside the conventional sensor housing. This structure is more suitable for detecting occasions where the installation space is limited.
adjust
Almost all ultrasonic sensors can adjust the proximity and distance of the switch output or the measurement range. Objects outside the set range can be detected but will not trigger changes in the output state. Some sensors have different adjustment parameters, such as response time, echo loss performance of the sensor, and setting adjustment of the working direction when the sensor is connected with the pump device.
Repeatability
Wavelength and other factors will affect the accuracy of ultrasonic sensors. The most important factor is the temperature
Ultrasonic sensor
With varying sound velocity, many ultrasonic sensors have temperature compensated characteristics. This feature enables analog output ultrasonic sensors to achieve repeatability of up to 0.6mm over a wide temperature range.
Output function
All series of ultrasonic sensors have switching output products. Some products also have 2 switching outputs (such as minimum and maximum level control). Most product lines offer products with analog current or analog voltage output.
Noise suppression
Noises such as metal knocking and roaring do not affect the parameter assignment of the ultrasonic sensor. This is mainly due to the optimization of the frequency range and the patented noise suppression circuit.
Synchronization function
The synchronization function of the ultrasonic sensor prevents interference. They enter into their synchronization lines by
Ultrasonic sensor
Simple connection to achieve synchronization. They simultaneously emit acoustic pulses that work like a single sensor while having an extended detection angle.
Alternate work
Ultrasonic sensor long scan type
Ultrasonic sensors working in an alternating manner are independent of each other and do not interfere with each other. The more sensors that work in an alternating manner, the lower the switching frequency of the response.
Detection conditions
Ultrasonic sensors are particularly suitable for working in "air" media. This sensor can also work in other gaseous media but requires sensitivity adjustments.
Blind area
The direct reflection type ultrasonic sensor cannot reliably detect some objects located in the front stage of the ultrasonic transducer. Thus, the area between the ultrasonic transducer and the starting point of the detection range is referred to as a blind zone. The sensor must remain unblocked in this area.
Temperature and humidity
Air temperature and humidity can affect the travel time of sound waves. Every 20°C rise in air temperature, the detection distance increases by up to 3.5%. Under relatively dry air conditions, an increase in humidity will result in a 2% increase in the speed of sound.
air pressure
Under normal circumstances, atmospheric changes of ± 5% (selecting a fixed reference point) will result in a ± 0.6% change in the detection range. In most cases, the sensor will work without problems under 5 Bar pressure.
airflow
Changes in airflow will affect the speed of sound. However, the effect caused by the airflow speed up to 10 m/s is negligible. Under the prevailing conditions of generating eddy currents, for example, for hot metal, it is not recommended to use an ultrasonic sensor for the detection because it is very difficult to calculate the echo of the distorted acoustic wave.
Standard test object
A square acoustic reflector is used for nominal switch distance sn calibration.
1mm thickness
Verticality: perpendicular to the beam axis.
Protection level
The shell can be protected against solid particles and watertight.
IP65: Completely dust-proof; penetration of waterproof posts.
IP67: It is completely dustproof; it can be effectively protected by immersing it in a depth of 1m under the constant temperature for 30 minutes.
IP69K: DIN 40050-9 based on EN60529
Pump function
Dual position control can be implemented, such as the pump-in function of a level control system. When a measured object is far away from the sensor and reaches the far point of the detection range, the output action is performed. When the measured object approaches the sensor and reaches the near point set in the detection range, the opposite action is output.
The ultrasonic sensor is mainly composed of the following four parts:
Transmitter: Vibration is generated by vibrators (usually ceramics, approximately 15 mm in diameter) and transmitted to the air.
Receiver: When the vibrator receives the ultrasonic wave, corresponding mechanical vibration occurs according to the ultrasonic wave, and it is converted into electric energy as the output of the receiver.
Control section: The ultrasonic wave transmission of the transmitter is controlled by the integrated circuit, and it is judged whether the receiver receives the signal (ultrasonic wave) and the size of the received signal.
Power section: Ultrasonic sensors are usually powered by DC12V ± 10% or 24V ± 10% external DC power and are supplied by the internal voltage regulator circuit.
According to the characteristics of the detected object's volume, material, and whether it can be moved, ultrasonic sensors use different detection methods. The common detection methods are as follows:
Penetration: The transmitter and the receiver are located on both sides. When the object to be detected passes between them, the detection is performed according to the attenuation (or shielding) of the ultrasound.
Limit distance type: The transmitter and the receiver are located on the same side. When there is a detected object within a limited distance, the detection is based on the reflected ultrasonic wave.
Limited range type: The transmitter and the receiver are located in the center of the limited range. The reflector is located at the edge of the limited range, and the attenuation value of the reflected wave when no object is obstructed is used as the reference value. When the object to be detected passes within a limited range, it is detected based on the attenuation of the reflected wave (comparison of the attenuation value with the reference value).
Retro-reflective: The transmitter and receiver are located on the same side to detect the object (planar object) as a reflection surface and detect it according to the attenuation of the reflected wave.
Ultrasonic sensors with multimeters directly test nothing. To test the quality of the ultrasonic sensor, an audio oscillator circuit can be used. When C1 is 390OμF, an audio signal of about 1.9kHz can be generated between the 8 and 10 pins of the inverter. The ultrasonic sensor to be detected (transmitting and receiving) is connected between feet 8 and 10; if the sensor can emit an audio sound, it can basically be determined that it is better than the ultrasonic sensor.
Note: When C1=3900μF, it is about 1.9kHZ; when C1=0.O1μF, it is about 0.76kHZ.
The basic principle of ultrasonic liquid level measurement is that the ultrasonic pulse signal emitted by the ultrasonic probe propagates in the gas and is reflected after encountering the interface between air and liquid. After the echo signal is received, the propagation time of the ultrasonic round trip can be calculated. Convert distance or level height. Ultrasonic measurement methods have many other advantages that are incomparable to other methods: (1) No mechanical transmission parts, no contact with the measured liquid, non-contact measurement, no fear of electromagnetic interference, no fear of strong corrosive liquids such as acid and alkali, and therefore performance Stable, high reliability, long life; (2) The short response time can facilitate real-time measurement without hysteresis.
The operating frequency of the ultrasonic sensor used in the system is about 40 kHz. An ultrasonic pulse is emitted from the transmitting sensor, transmitted to the liquid surface and reflected back to the receiving sensor, and the time required for the ultrasonic pulse to be transmitted from receiving to receiving is measured. According to the speed of sound in the medium, the distance from the sensor to the liquid surface can be obtained. To determine the liquid level. Taking into account the impact of the ambient temperature on the ultrasonic propagation speed, the propagation speed is corrected by the temperature compensation method to improve the measurement accuracy. The formula is:
V=331.5+0.607T (1)
Where: V is the speed of ultrasonic wave propagation in the air; T is the ambient temperature.
S=V ×t/2=V×(t1-t0)/2 (2)
Where: S is the distance to be measured; t is the time difference between the transmitted ultrasonic pulse and its echo; t1 is the ultrasonic echo reception time; t0 is the ultrasonic pulse transmission time. Using the capture function of the MCU can easily measure t0 time and t1 time. According to the above formula, the distance S can be measured by software programming. Since the MCU of the system selects a mixed-signal processor with SOC characteristics and integrates a temperature sensor therein, the temperature compensation of the sensor can be easily implemented using the software.
The difference between ultrasonic sensors and sonar sensors
Sonar sensors and ultrasonic sensors are two kinds of detection devices that are often heard. Many people think that these two types are sensors. What is the difference between these two types of sensors?
The sonar sensor directly detects and recognizes the outlines of underwater objects and waters. The sonar sensor emits a sound wave signal, which is reflected when the object is encountered.
Come, calculate its distance and position according to reflection time and wave type. Ultrasound is a kind of mechanical wave whose vibration frequency is higher than that of sound waves. It is generated by transducers vibrating under the excitation of voltage. It has high frequency, short wavelength, and small diffraction phenomenon, especially good directionality, which can become ray and orientation. Dissemination and other characteristics. The sonar sensor is mainly used for detecting organisms, for example, what kind of organisms are detected on the bottom of water, and how large the organism is. The device used to detect the monsters that you often hear is the sonar sensor.
Ultrasonic penetration of liquids, solids is very large, especially in the opaque solid, it can penetrate depths of tens of meters. Ultrasonic waves that encounter impurities or interfaces can produce significant reflections and reflect back into echoes, and Doppler effects can occur when moving objects are encountered. Therefore, ultrasonic testing is widely used in industrial, national defense, and biomedical fields. Ultrasonic sensors are sensors developed using the characteristics of ultrasound. In industry, the typical application of ultrasonic is two kinds of non-destructive testing of metal and ultrasonic thickness measurement. The application of ultrasonic sensors in medicine is mainly to diagnose diseases. It has become an indispensable diagnostic method in clinical medicine. [3]
1: To ensure reliability and long service life, do not use the sensor outdoors or at temperatures higher than the rated temperature [4] .
2: Because the ultrasonic sensor uses air as the transmission medium, when the local temperature is different, the reflection and refraction at the boundary may cause malfunctions, and the distance detected when the wind blows will also change. Therefore, sensors should not be used near devices such as forced draft fans.
3: The air jet ejected by the air jet has a variety of frequencies and therefore affects the sensor and should not be used near the sensor.
4: Drops of water on the sensor surface shorten the detection distance.
5: Materials such as fine powder and cotton yarn cannot be detected when absorbing sound (reflective sensor).
6: The sensor cannot be used in a vacuum area or an explosion-proof area.
7: Do not use the sensor in areas with steam; the atmosphere in this area is not uniform. Temperature gradients will occur, which will lead to measurement errors.
Exposure issuesUltrasonic sensors are simple to use, very convenient, and cost-effective. However, current ultrasonic sensors have some drawbacks, such as reflection problems, noise, and crossover problems.
Reflection problem
If the detected object is always at the right angle, the ultrasonic sensor will get the correct angle. Unfortunately, rarely detected objects are detected correctly in actual use.
There may be several types of errors:
Triangular error
When the measured object is at an angle to the sensor, there is a trigonometric error between the detected distance and the actual distance.
reflection of mirror
This problem is the same as the reflection of light learned in high school physics. At a particular angle, the emitted sound waves are mirrored off of the smooth object, so no echo can be generated and no distance readings can be produced. At this time, the ultrasonic sensor ignores the presence of this object.
Multiple reflection
This phenomenon is common when detecting corners or similar structures. The sound wave is received by the sensor after multiple bounces, so the actual detection value is not the actual distance value.
These problems can be solved by using a plurality of ultrasonic coils arranged at a certain angle. By detecting the return value of multiple ultrasonic waves, it is used to filter out the correct reading.
noise
Although most ultrasonic sensors operate at 40-45 kHz, they are much higher than humans can hear. However, the surrounding environment can also produce similar-frequency noise. For example, when the motor rotates, it will generate certain high frequencies, the high-frequency noise generated by the friction of the wheels on harder ground, the vibration of the robot itself, and even when there are multiple robots, the sound waves emitted by other robot ultrasonic sensors. This will cause the sensor to receive the wrong signal.
This problem can be solved by encoding the emitted ultrasonic waves, such as emitting a group of different wavelengths. The distance calculation is performed only when the probe detects the same combination of sound waves. This can effectively avoid misreading due to environmental noise.
Crossover problem
The crossover problem is caused when multiple ultrasonic sensors are mounted on the robot at an angle. The sound waves emitted by the ultrasonic X are reflected by the mirror and obtained by the sensors Z and Y. Then Z and Y will calculate the distance value based on this signal, and the correct measurement cannot be obtained.
The solution can be to encode the signal from each sensor. Let each ultrasonic sensor only listen to its own voice.
Reference editing area
Powder Mixing Machine,Industrial Powder Plough Mixer,Cake Mix Plow Knife Mixer,Dehydrated Vegetable Plow Knife Mixer
Jiangyin Longchang Machinery Manufacturing Co,Ltd , https://www.jylongchanggrinderline.com